Mechanical Engineering Research Areas
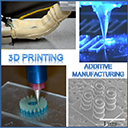
3D Printing of Smart Structures
The Advanced Additive Manufacturing Lab (AAML) was established in spring 2011 with various 3D printing capabilities. AAML is investigating new 3D printing processes with multi-material, multi-scale capabilities. In addition to processes, the lab is also working on various 3D-printable materials including polymer, ceramic, metal, and their composites. With these new processes and materials, we are extending applications to artificial skins, all-solid-state batteries, supercapacitive batteries, structural electronics, smart insoles/tires, robotic grippers, airless tires, etc. More...
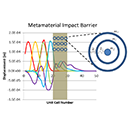
Acoustic/Elastic Composite Metamaterials
Acoustic/elastic composite metamaterials exhibit unique properties not commonly found in natural materials. By specially designing their microstructures, these metamaterials possess negative effective mass density over certain frequency ranges. This implies that stress waves cannot be transmitted through the material, thus enabling control and attenuation of stress wave propagation. This results in interesting applications including vibration control, impact protection, blast wave mitigation and energy harvesting. More...
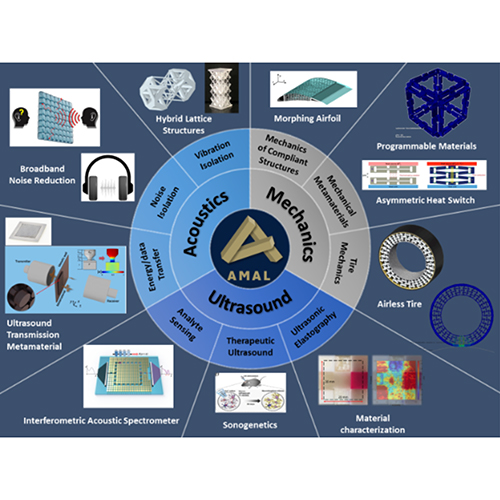
Advanced Mechanics and Acoustics Lab
The Advanced Mechanics and Acoustics Lab (AMAL) specializes in metamaterials, acoustic engineering, and advanced mechanical systems. Past work includes developing acoustic metasurfaces for automobile tire-road noise reduction and exploring non-reciprocal wave propagation. Current research focuses on innovative material design across multiple domains, including programmable materials, ultrasound transmission metamaterials, and hybrid lattice structures. Our mission is to design the adaptive, intelligent materials that will redefine future technologies. More...
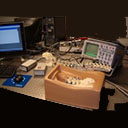
Autonomous Systems Laboratory
The laboratory is home to research in robotics, intelligent systems, controls, structural health monitoring, biomedical devices and low-cost remote monitoring platforms. Past work includes brake modeling for Formula One race teams, intelligent monitoring of rocket tests for NASA and design of biomedical devices in the areas of neurosurgery and urology. Current work focuses on developing low-cost monitoring devices based on the Arduino/Raspberry platforms that can be used in multiple verticals such as genomics, food production, water purification and reduction of healthcare costs. More...
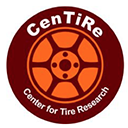
Center for Tire Research (CenTiRe)
Working within the NSF I/UCRC program CenTiRe performs industrially-relevant, pre-competitive research via multi-member, sustained partnerships among industry, academe, and government. As the only tire research center within this NSF program, CenTiRe is uniquely positioned to provide its members a cost-effective means to access technical advancement and trained students in the areas of tire and tire related materials, modeling, testing, and manufacturing. More...
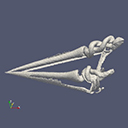
Computational Aerodynamics
The group’s research efforts are in the emerging areas of computational fluid dynamics (CFD) including vorticity confinement approach for accurate prediction of vortices and aerodynamic drag in air vehicles supported by AFRL, ARO, Navy SBIR and NSF. Other funded projects include coupled molecular and continuum modeling of micro- and nano- fluids in chemical vapor deposition processes, ablation of thermal protecting shield in hypersonic flight and modeling of explosions in offshore oil drilling. More...
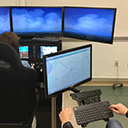
Human Factors Engineering Lab
The Human Factors Engineering Lab studies the complex interactions between human operator and other system elements in order to enhance system safety and efficiency. Our lab perform research in cognitive system engineering and human decision making in the aviation systems, severe weather forecasting systems, healthcare systems. The lab receives funding from NOAA, FAA, and private industry. The lab director Dr. Chen Ling is also the director of FAA Center of Excellence for Technical Training and Human Performance at University of Akron.
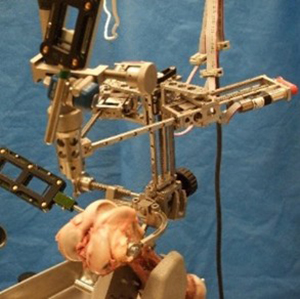
Interventional Robotics Laboratory
IRL focuses on developing robotic systems and biomedical devices to enable new medical interventions and enhance safety and efficacy. Current projects include robotic orthopedic surgery, MRI-guided prostate biopsy and focal therapy, semi-robotic laparoscopic and arthroscopic surgery, tactile display for advanced telemedicine, and soft robotic systems for surgery and healthcare. More...
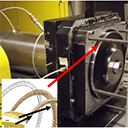
Joint Laboratory for Flow Visualization and Lubrication (LFVL)
The LFVL houses state of the art laser and PIV equipment for non-intrusively visualizing flow and temperature patters in forced as well as natural convection flows. Using long distance microscopy flows can be studied in enclosures as small as 25 microns (MEMS cooing, bearings and seals). The laboratory also houses two high speed (60 krpm) spindle testbeds (40 and 200 HP respectively) for evaluation of performance high speed bearings and contacting and non-contacting seals (brush seals and finger seals). The of the laboratory researchers (faculty and students) have innovated in the area of metal lubricated bearings with self circulation, non-contacting finger seals, in-line debris health monitoring, and intelligent controllable bearings and seals.
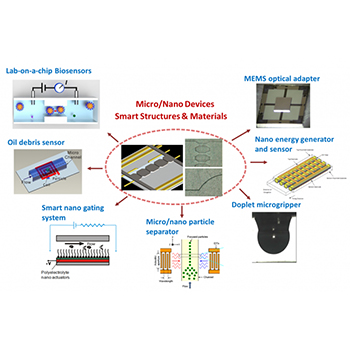
Micro Electro Mechanical Systems Lab
Micro Electro Mechanical Systems (MEMS) Research Lab at University of Akron utilizes smart micro and nano structures to realize unprecedent functions for various applications. These applications include biosensors for clinical use, micro sensor array for machine health monitoring, smart nano gating systems for molecular machine, micro gripping for micro robots, micro devices for energy harvesting and optical communications. In particular, MEMS lab has been engaged in the following applications: 1) Microfluidic and nanofluidic devices and instruments that can detect biomarkers and rare cells with ultra low concentrations, which can thus provide prognosis of diseases (e.g. cancer), environment protection, anti-terrorism, as well as a variety of biomedical application (e.g. tissue engineering) ; 2) AI based microsensor array for online machine health monitoring, which can provide real time properties of machine’ blood, its lubricant, and therefore provide machines’ health status. More...
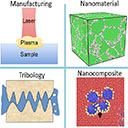
Micro/Nano Engineering Lab
We apply theoretical and numerical methods to solve engineering problems at micro and nano scale. Atomistic modeling (Density Functional Theory, Molecular Dynamics Simulation and Lattice Dynamics), statisticial modeling (Boltzmann Transport Equation and Monte Carlo Method) and continuum modeling (Finite Differential/Volume/Element Methods) are employed to investigate mechanical, thermal and electrical properties of materials. More...
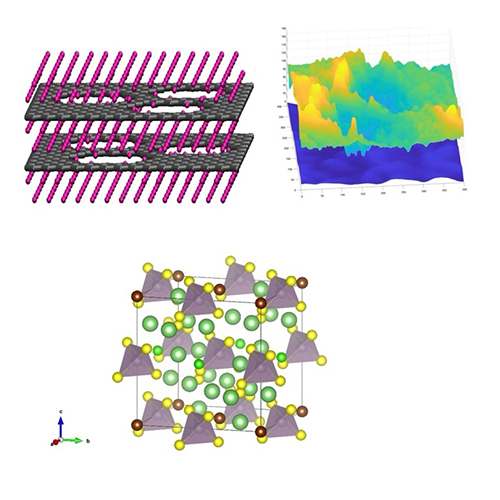
Modelling and Design of Advanced Materials at the Nanoscale
We perform atomistic and continuum modeling and simulations of advanced materials at the nanometer length scales. Our research topics include modelling and design of solid electrolytes for solid state Li ion batteries. Recently, nanoporous graphene has attracted great interest in the scientific community. We study the lithium-ion adsorption mechanism in nanoporous graphene. Nanoscale adhesion and friction is another research topic area. We investigate tire rubber – road adhesion and friction at the nanoscale. More...
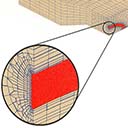
Multi-scale Modeling of Damage and Failure of Materials
Computational solid mechanics. Constitutive modeling of advanced materials. Nonlinear fracture mechanics. Constraint effect and toughness scaling. Multi-scale modeling of damage and failure of composite materials. Mechanism-based approaches to simulate material failure process and to predict fracture of structural components. Fatigue life prediction. More...
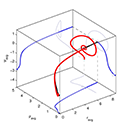
Nonlinear Dynamics and Structural Mechanics
This research area focuses on the investigation of the dynamical response of nonlinear engineering systems, with application to the areas of vibrations and dynamical systems, contact dynamics and control theory, and an underlying theme is the understanding of these systems through the development and analysis of simplified models. More...
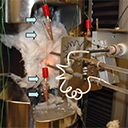
Performance, Failure Mechanisms and Life of High Temperature Composites
Microstructural-based understanding of mechanical performance of ceramic fiber-reinforced ceramic matrix composites. Damage detection and health-monitoring techniques such as acoustic emission and electrical resistivity for composites, structures (e.g., joining and integration of dissimilar materials), and machines. Work with NASA, Air Force, Navy, Goodrich, aero engine companies, and small businesses (SBIR and STTR). More...
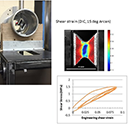
Solid Mechanics
Composite structures; sandwich structures; elastomers; blast and impact mechanics; fluid-structure interaction; damage modeling; FEA. Current interests in the use of foam-core composite sandwich panels for underwater blast mitigation; polymer foam constitutive modeling; multi-scale, damage modeling for FEA simulation of filled rubbers. More...
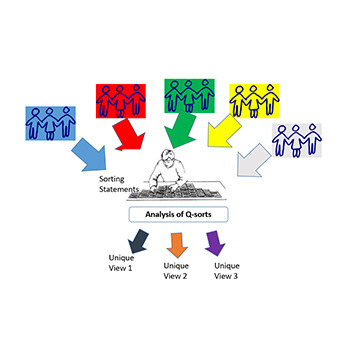
STEM Education Research
Susan Ramlo's research focuses on STEM education and the use of Q methodology to explore perspectives in higher education. Her work examines the experiences of students and faculty in STEM fields, emphasizing problem-based learning, curriculum development, and interdisciplinary collaboration. She applies Q methodology within mixed methods research to better understand subjective viewpoints related to STEM learning and teaching. Her research also connects to broader discussions in the philosophy of science and psychometrics, particularly in relation to how meaning is constructed within educational settings. Through her work, she contributes to improving STEM education and informing institutional decision-making.
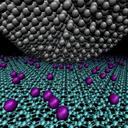
Surface Engineering and Advanced Manufacturing
The SEAM group uses various surface processing techniques to engineer beneficial microstructure and/or residual stress changes on metal surfaces to improve the properties and performance. We integrate experiment with multiscale simulation to explore the processing-structure-property relationships. More...
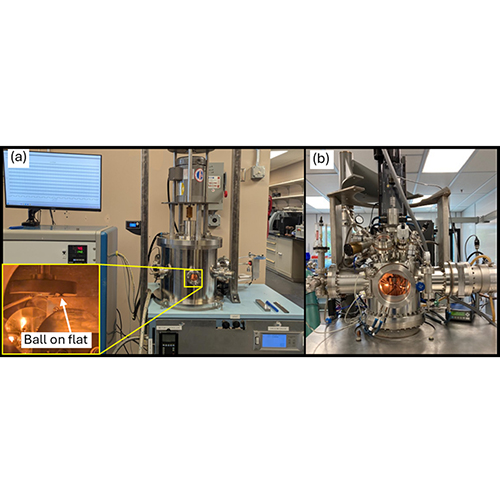
Tribology (Friction and Wear)
Tribology is the study of friction, wear and lubrication. The word Tribology comes from the Greek word “tribos” which means “to rub”. The University of Akron has a long history of conducting tribology research that supports local, national and international businesses and government organizations. In 2012, Timken, the State of Ohio and the University of Akron launched a comprehensive, state of the art tribology lab to educate students to do R&D and to prepare them to solve engineering challenges in their future careers. The Akron Engineering Tribology Lab (AETL) is comprised of 6,000 square feet of lab space that includes a clean room in which bearings are tested at high speed in vacuum at high temperatures simulating extreme environments as may be encountered in space. A unique high temperature, high vacuum multi-configuration pin-on-disk test machine is used to compliment the vacuum bearing rig. Rolling and sliding contacts are simulated in a wide variety of commercial bearing testers. Additional capabilities include comprehensive oil and grease characterization, detailed surface topographical measurements, atomic force microscopy (AFM), macro and nano indentation hardness testing, and advanced spectroscopic techniques such as Raman spectroscopy, X-ray fluorescence (XRF), and Fourier Transform infrared (FT-IR) spectroscopy. Current projects include space and medical product tribology, water-based lubricants for electric vehicle motor bearing tribology, grease migration studies, gas compression and petroleum (downhole) extraction equipment friction and wear studies, and steel mill bearing tribology.
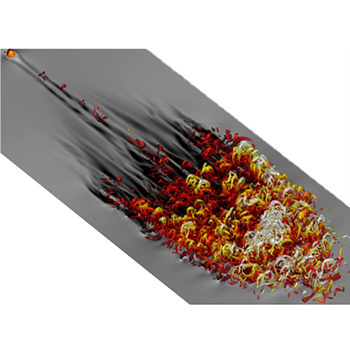
Turbulence and Flow Control Laboratory
The turbulence and flow control laboratory studies unsteady, transitional, and turbulent flow relevant to mechanical and aerospace engineering applications using high-fidelity computer simulations. The mechanistic understanding of the underlying flow physics is used to engineer novel flow control solutions. Examples include AFOSR-sponsored research on boundary layer transition mitigation using surface textures and NSF-sponsored research on separation control by selective manipulation of large-scale coherent structures and advancing stall alleviation on airfoils using enhanced vortex generators. Target applications include the aerodynamics of urban mobility and unmanned aerial vehicles operating in inclement weather. The lab also studies fluid-structure interactions and multiphase flows relevant to manufacturing processes. More...